Quality Control Laboratory
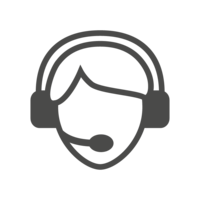
Maintaining Quality Standards
Printing and packaging must have optimal quality to ensure final products meet customer expectations. Quality control tests determine whether raw materials, ink, printing, and packaging processes comply with established standards.
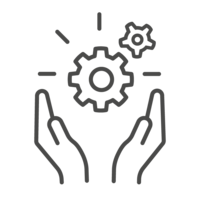
Preventing Resource Waste
In printing and packaging processes, quality deficiencies cause production errors that lead to additional costs, raw material waste, and reduced productivity. Quality control enables early defect identification and prevents mass production of defective products.
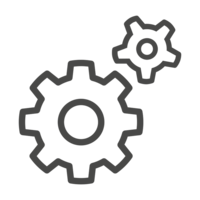
Environmental Alignment and Sustainability
Tests can ensure the accuracy of raw materials and environmental impacts of production processes, which is crucial given OJENILI's commitment to sustainability.
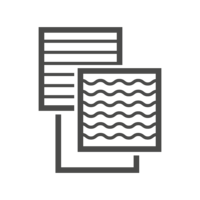
Evaluating Technical Packaging Characteristics
Packaging must be robust, attractive, and standardized to withstand various environmental conditions and protect the product. Quality control includes assessments that ensure packaging is not only beautiful but also resilient and compatible with transportation and storage conditions.
OJENILI Quality Control Laboratory: Quality Assurance in Packaging and Printing
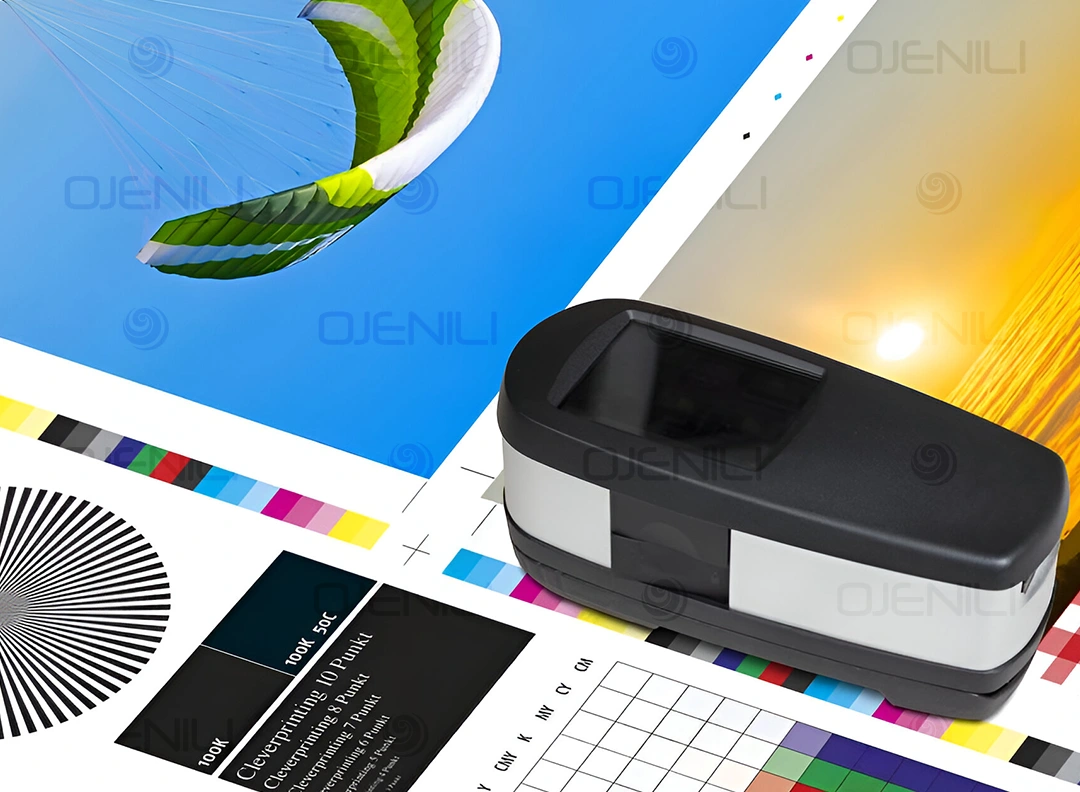
The Quality Control Laboratory of the OJENILI Printing and Packaging Complex, as part of the production process, performs the most precise tests from the beginning to the end of each packaging and printing project to ensure that the final products reach customers with the highest quality standards. In today's competitive world, quality and durability in packaging and commercial printing play a key role. OJENILI Laboratory, by employing the latest laboratory equipment and a specialized team, has created ideal and reliable conditions for producing various packaging, labels, and commercial prints.
Why is Quality Control Important in Printing and Packaging?
High-quality printing and packaging not only enhances the visual appeal of products but also protects the product from potential damage and increases the product's lifespan. The OJENILI Quality Control Laboratory examines all packaging and printing products in terms of aspects such as color accuracy, print clarity, packaging strength, and compliance with environmental standards.
Specialized Services of OJENILI Quality Control Laboratory
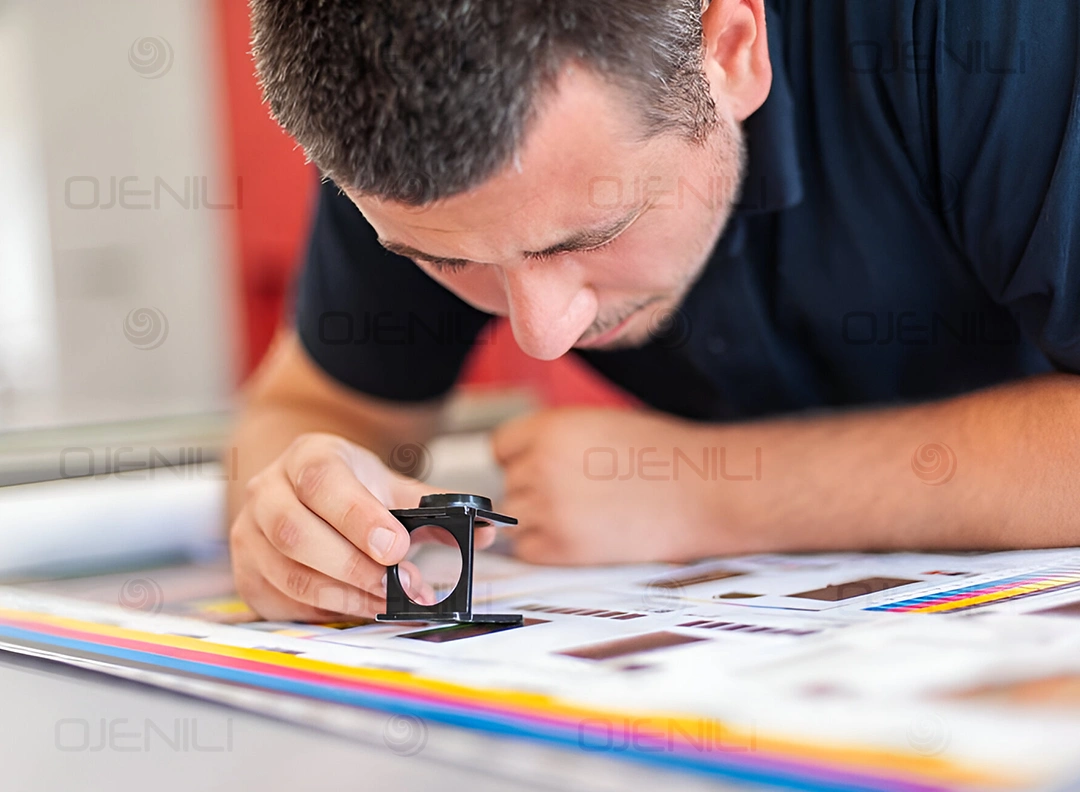
1. Raw Material Quality Assessment: Raw materials used in the printing and packaging process such as paper, cardboard, plastic, and printing inks are precisely tested to ensure their compliance with global standards.
2. Printing and Packaging Resistance Testing: Commercial prints and packaging must be able to withstand various conditions such as humidity, light, and high temperature. The OJENILI specialized team guarantees the quality and durability of packaging and labels through simulated condition tests.
3. Compliance with Environmental Standards: In line with commitment to sustainability, specific tests are conducted to evaluate renewable and recyclable materials and assess the environmental impacts of packaging.
4. Final Quality Control: Products are carefully examined before final delivery to ensure no defects exist and that the final product reaches the customer at the highest quality.
Importance of OJENILI Quality Control Laboratory for Customers
With its expertise and advanced facilities, the OJENILI Quality Control Laboratory assures all customers that the final products are precisely manufactured according to their needs and established standards. As one of the largest printing and packaging complexes, through quality control tests, this facility enables the production of durable, resistant, and beautiful products, ensuring customers of the quality and sustainability of the products.
1. Raw Material Quality Assessment
More details:
In this section, raw materials such as paper, cardboard, ink, and packaging materials are meticulously tested before use in the printing and packaging process. Tests such as thickness, tensile strength, moisture absorption, and coloration are performed on raw materials. The goal is to ensure the compliance of these materials with international standards and specific customer requirements.
Factors involved from customer and intermediate manufacturer perspectives:
• Stability and Durability of Materials: Customers and intermediate manufacturers are typically concerned about the durability and lifespan of packaging. Low-quality materials can damage the product and reduce its useful life.
• Ink Coloration and Permanence: Audiences expect colors on packaging to be precise, clear, and permanent, not fading or changing over time.
• Material Resistance to Various Environmental Conditions: Intermediate manufacturers and end-users want packaging and prints to be resistant to conditions like humidity, sunlight, and high temperatures.
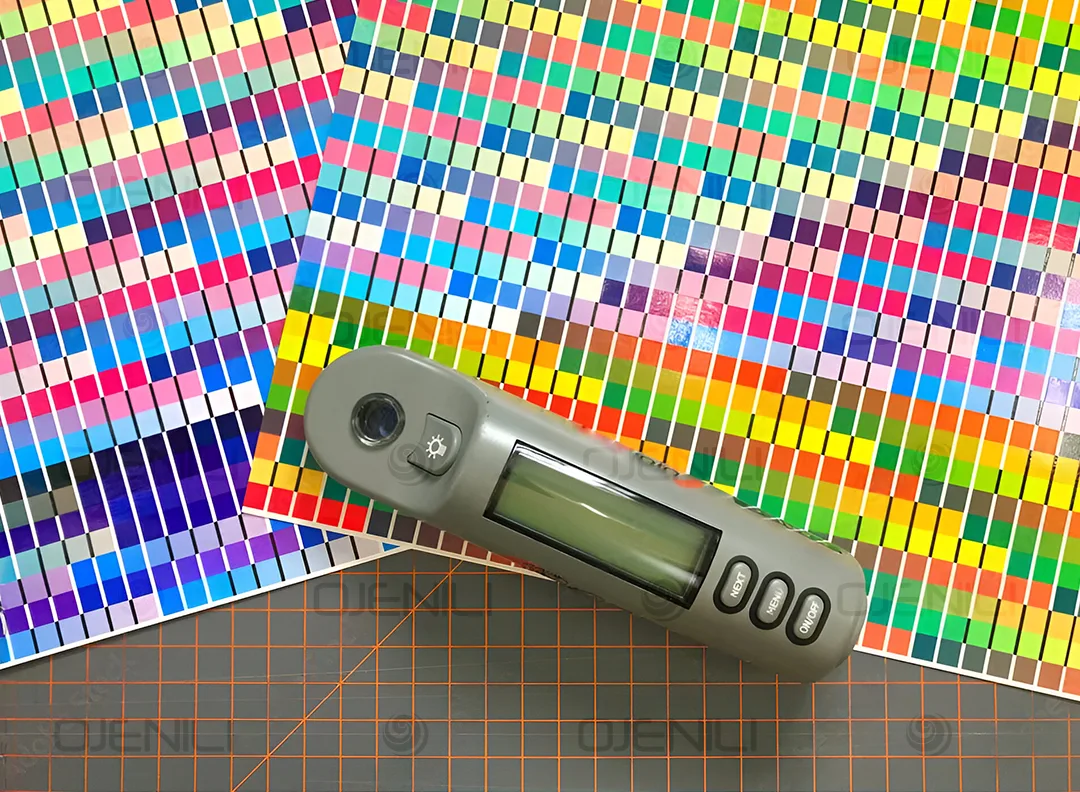
2. Printing and Packaging Resistance Testing
More details:
Prints and packaging undergo simulated tests to evaluate resistance and durability. These tests include assessing packaging resistance to impact, scratching, pressure, and even moisture and temperature conditions. This section ensures that products maintain their integrity under various conditions throughout the distribution and storage chain without damaging the product.
Factors involved from customer and intermediate manufacturer perspectives:
• Physical Strength of Packaging: Customers expect packaging to be resistant to pressure and impact to prevent product damage during transportation.
• Print Resistance to Scratching and Abrasion: Scratched and worn packaging reduces visual appeal. This is especially important in luxury and consumer industries where customers care about appearance.
• Stability of Printing and Packaging in Humid and Hot Environments: For products stored in shops and warehouses, maintaining print quality in humid and hot conditions is crucial.
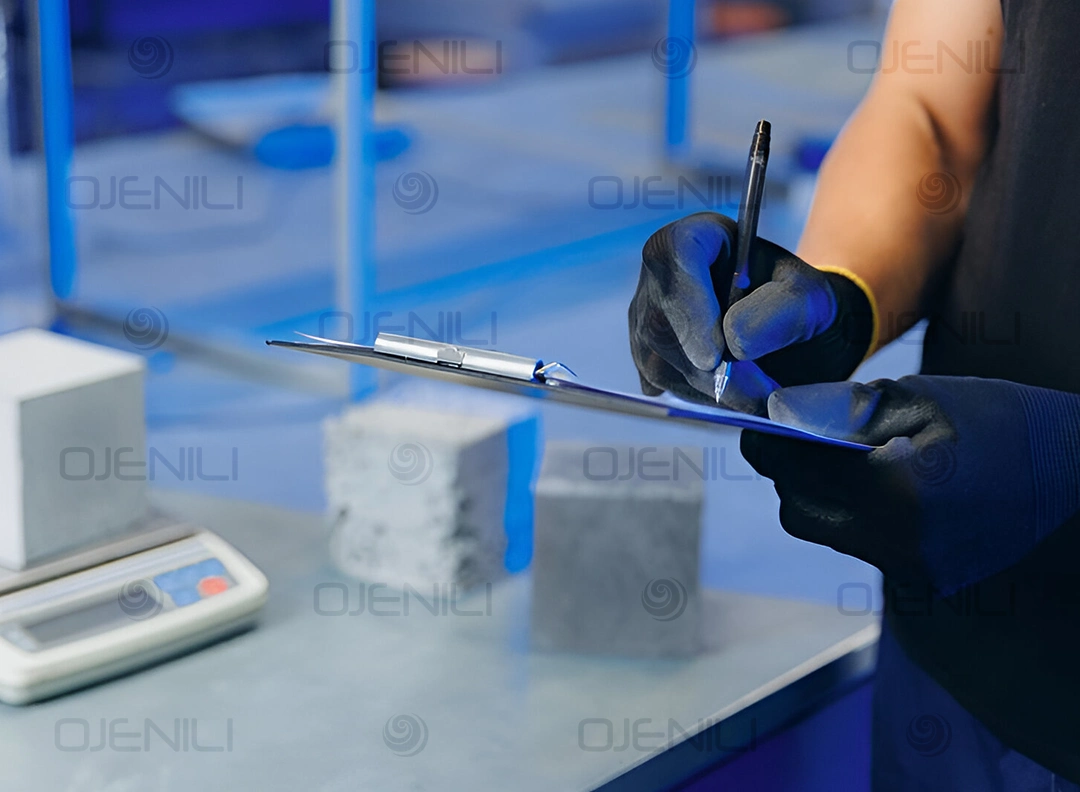
3. Compliance with Environmental Standards
More details:
OJENILI Laboratory uses renewable and recyclable materials in packaging and implements production processes focused on reducing waste and preserving natural resources. These tests specifically examine the environmental impacts of materials used in packaging and their environmental compatibility.
Factors involved from customer and intermediate manufacturer perspectives:
• Use of Recyclable and Renewable Materials: Brands committed to the environment expect printing houses to use environmentally friendly raw materials and processes.
• Reducing Carbon Footprint and Production Waste: Some customers seek to reduce carbon emissions and optimize resource consumption in the production process, considering this in choosing a printing partner.
• Responding to Environmental Standards and Required Permits: Printing and packaging products must align with local and international environmental standards.
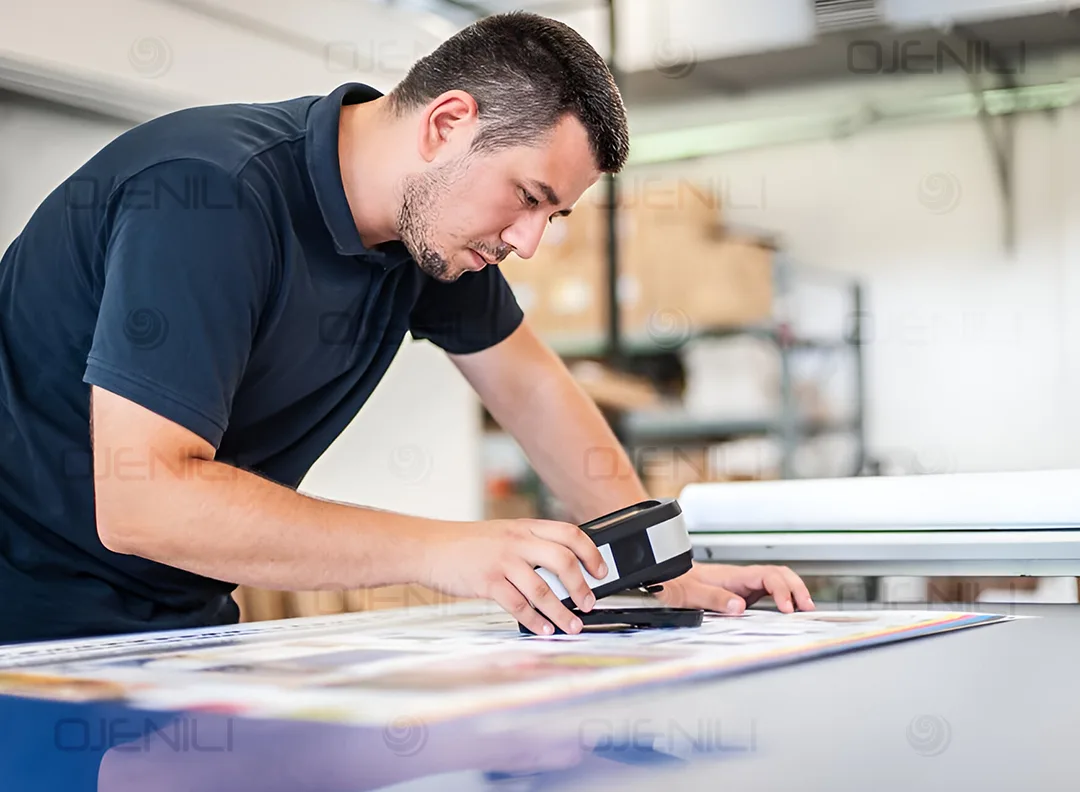
4. Final Quality Control
More details:
In the final quality control section, completed and packaged products are carefully examined before final delivery to ensure their integrity, quality, and flawlessness. This stage is the last opportunity to identify and rectify any potential issues in packaging and printing. Visual and digital inspection tools are used to check precise color synchronization, print defect-free status, and complete alignment with customer requirements.
Factors involved from customer and intermediate manufacturer perspectives:
• Final Review of Print Quality and Compliance with Initial Design: Intermediate manufacturers and end customers want print and packaging quality to match the initial design and standards.
• Color and Print Uniformity Across All Products: In large orders, customers seek uniformity and lack of variation in printing and colors.
• Final Inspection and Absence of Defects like Stains, Bubbles, or Scratches: Surface defects in packaging and printing can damage the brand and lead to customer dissatisfaction.